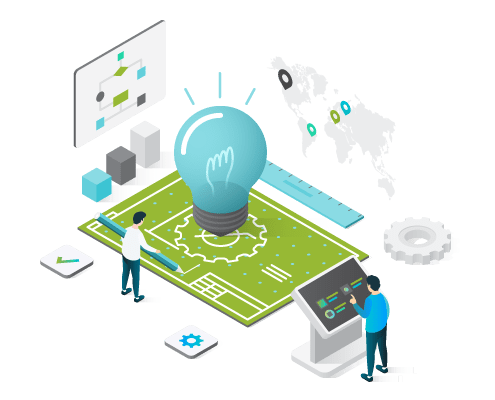
A US based retailer relocated its supply base and needed help resolving quality and capacity issues.
Challenge
A US based customer from the retail industry had its supply base move from China to another AP region and had quality issues and capacity issues. Quality Requirements of the US/European Market were not understood by new suppliers. There were several rejections from its new suppliers & it was running out of inventory to serve the market. The customer needed immediate support locally in Vietnam to help its supplier improve the quality of the product as an immediate action and develop the robust quality management system as a long-term strategy.
The retailer approached and partnered with Empower QLM to develop its supply base in Vietnam.
Solution
Quality Services & Strategy
The customer requirements were immediately worked on & quick response supplier quality teams were allocated with a high level of Problem Solving & sheet metal/welding commodity experts to go onsite. The team was tasked with creating a roadmap for project execution. The team worked onsite for almost 8 weeks and brought the supplier’s daily production levels back to normal.
The Team conducted Process Audit and identified around 60 action items(gaps) to implement and developed a road map for execution. Identified defects types and arrived at the Root cause and provided suggestion to improve and reduce rejections. It also Developed welding fixture designs for the supplier using the R&D center, Closed all action items, improved the First pass yield, Reduced Scrap rate, and reduced Cost of Poor Quality (CoPQ). In addition, the team provided extensive hands on training on right and wrong manufacturing processes to graduate the skill level of employees. A system and reporting were created to effectively monitor the process yields, root cause analysis & corrective actions. KPI’s were monitored offshore for about 2-3 weeks until the supplier reached its target and the retail customer gained confidence.
The welding operators and managers were trained while working on work instructions and process improvements.
Benefit
The quick and timely rapid response quality team was helpful to contain the issue and bring back the products on empty shelves in the store.
By having a dedicated onsite team as ears and eyes and boots on the ground, the customer had full control over its supplier without using its own resources & time. The customer was successful in getting defect free products and met production capacity and had sufficient inventory. It also Improved is supplier by providing understanding of customer requirements & deep quality management practices. With the success of this program, the reliable partnership improved the quality of the new supply base across AP region.