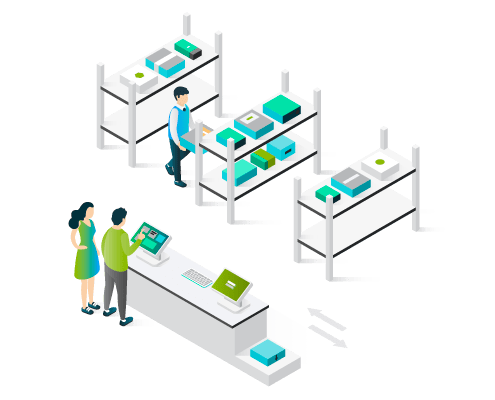
A Tier 1 global automotive driveline and powertrain customer from the US needed solutions for implementation of APQP including PPAP approvals.
Challenge
A Tier 1 global Automotive driveline and powertrain customer from the US was looking for low cost solutions for implementation of APQP including PPAP approvals and the management of the timelines for these activities. Also, the customer’s challenge was to coordinate with global suppliers in different time zones from USA, Europe, and Asia locations.
Solution
Quality Services & Training
A few Global Technical Center SQE resources from India are allocated for different time zones and work remotely. These SQE are strong in communication and experienced with Automotive AIAG, APQP, and PPAP approval processes. The dedicated team of SQEs were trained on using the customer’s supplier portal for APQP activities and technical documents requirements. The SQEs coordinated with suppliers to provide APQP trainings and worked with the suppliers for development of 27 elements in APQP activities as well as standardization of supplier documentation process in APQP activities including PPAPs. With this support, the APQP timeline and on-time PPAP approvals was met. Finally, the customer plants’ approved the PPAPs. This support has been ongoing for the last 3 years.
Benefit
The customer benefitted by having complete control of its APQP activities including its PPAP approvals. Using the India center, the cost of operations was reduced more than 50%. The customer achieved its timelines and deliverables in timely manner. The process of APQP and PPAP was streamlined and standardized for long term benefits. As part of the process, several recommendations and improvements were made in the process. The customer’s internal SQE resources were able to do much more valuable work and contribute to other hot and urgent areas of product development activities and continual improvement activities.